Understanding Airflow Control in Softwall Cleanrooms for Effective Contamination Control
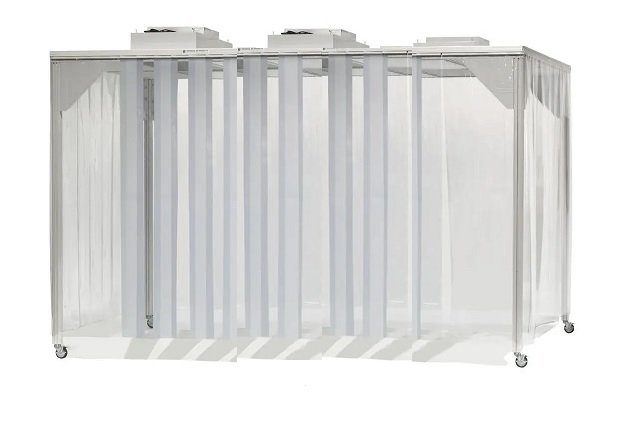
In the realm of controlled environments, cleanrooms play a pivotal role in ensuring the highest levels of contamination control. They are indispensable in industries like pharmaceuticals, electronics manufacturing, biotechnology, and aerospace, where even the tiniest particles or microorganisms can lead to disastrous consequences. Among the various cleanroom types, softwall cleanrooms have gained popularity due to their flexibility, cost-effectiveness, and ease of installation. A fundamental component of any cleanroom, including softwall cleanrooms, is airflow control. This article, provided by Cleatech LLC, will delve into the intricacies of airflow control in softwall cleanrooms and elucidate its paramount importance in contamination control.
Section 1: Understanding Softwall Cleanrooms
Before delving into airflow control, it’s essential to understand what softwall cleanrooms are and how they differ from their hardwall counterparts.
1.1 What Are Softwall Cleanrooms?
Softwall cleanrooms, also known as curtain or flexible-wall cleanrooms, are controlled environments designed to maintain precise levels of cleanliness by regulating airborne particles, temperature, humidity, and other environmental parameters. Unlike hardwall cleanrooms, which have rigid walls made of materials like stainless steel or aluminum, softwall cleanrooms feature flexible walls typically composed of transparent or opaque vinyl curtains. These curtains are hung from a sturdy frame, creating a sealable enclosure that can be customized to suit various industry-specific needs.
1.2 Key Features of Softwall Cleanrooms
Softwall cleanrooms offer several advantages over their hardwall counterparts:
Flexibility: Softwall cleanrooms are highly adaptable, making them ideal for industries where configurations may change frequently.
Cost-Effective: They are often more budget-friendly than hardwall cleanrooms, both in terms of initial setup and ongoing maintenance.
Quick Installation: Softwall cleanrooms can be set up relatively quickly, reducing downtime during construction or reconfiguration.
Transparency: Transparent curtains allow visibility into the cleanroom, facilitating supervision and monitoring.
Customization: Softwall cleanrooms can be tailored to specific size, shape, and environmental control requirements.
Now that we have a basic understanding of softwall cleanrooms, let’s explore the crucial role of airflow control within these environments.
Section 2: Airflow Control in Softwall Cleanrooms
2.1 The Basics of Airflow Control
Airflow control in softwall cleanrooms involves the strategic management of the movement and circulation of air within the controlled environment. This process is essential for several reasons:
Contaminant Removal: Controlled airflow helps remove airborne particles, microorganisms, and contaminants from the cleanroom environment.
Temperature and Humidity Control: Proper airflow control aids in maintaining consistent temperature and humidity levels, which are critical in certain applications.
Worker Comfort: Adequate ventilation ensures that personnel working in the cleanroom remain comfortable during long shifts.
Energy Efficiency: Efficient airflow control can help reduce energy consumption by optimizing HVAC systems.
2.2 Key Components of Airflow Control in Softwall Cleanrooms
To achieve effective airflow control in softwall cleanrooms, several components and principles come into play:
HEPA Filters: High Efficiency Particulate Air (HEPA) filters are the cornerstone of cleanroom filtration. They capture particles as small as 0.3 microns, ensuring that the air entering the cleanroom is free of contaminants.
Supply and Exhaust Systems: Softwall cleanrooms are equipped with supply and exhaust systems that regulate the flow of clean, filtered air into the room and remove the contaminated air. The direction and velocity of airflow are carefully controlled to prevent cross-contamination.
Positive and Negative Pressure Zones: Softwall cleanrooms can be divided into positive and negative pressure zones to prevent contamination from entering or exiting specific areas. For example, pharmaceutical cleanrooms often maintain positive pressure to keep contaminants out, while microbiology labs use negative pressure to contain potential pathogens.
Airflow Patterns: The design of airflow patterns plays a crucial role in contamination control. Laminar flow, turbulent flow, or a combination of both can be employed, depending on the cleanroom’s requirements. Laminar flow, for instance, directs air in parallel streams, minimizing the chances of particle entrainment.
Monitoring and Control Systems: Modern softwall cleanrooms are equipped with sophisticated monitoring and control systems that continuously assess environmental parameters such as temperature, humidity, pressure differentials, and particle counts. Any deviations trigger automatic adjustments to maintain the desired conditions.
2.3 The Importance of Proper Airflow Control in Softwall Cleanrooms
Now, let’s delve into why airflow control is of paramount importance in softwall cleanrooms, focusing on its impact on contamination control.
2.3.1 Particle Contamination Control
Contamination in cleanrooms primarily occurs through the introduction of airborne particles. These particles can originate from various sources, including personnel, equipment, and the environment. Effective airflow control mitigates the risk of particle contamination by:
Dilution and Removal: Controlled airflow ensures that fresh, filtered air is continuously supplied to the cleanroom. This dilutes the concentration of particles and facilitates their removal through the exhaust system.
Directional Airflow: The direction of airflow is strategically designed to prevent particles from entering critical areas. For instance, in semiconductor manufacturing, laminar flow hoods direct clean air over sensitive wafer surfaces, minimizing the risk of particle deposition.
Containment of Contaminants: Negative pressure zones are used to contain contaminants within specific areas, preventing them from spreading to clean zones.
2.3.2 Microbial Contamination Control
In industries where microbial contamination poses a threat, such as pharmaceuticals and biotechnology, airflow control takes on even greater significance. Microorganisms like bacteria, viruses, and fungi can compromise product quality and pose health risks. Proper airflow control strategies for microbial contamination control include:
Sterile Environments: Softwall cleanrooms in these industries often maintain stringent conditions, such as positive pressure, to ensure that contaminants from the external environment cannot enter.
High-Efficiency Filtration: HEPA filters effectively capture microbial particles, preventing them from entering the cleanroom.
Personnel Training: Proper procedures for gowning and movement within the cleanroom are crucial to minimize the risk of introducing microorganisms.
2.3.3 Temperature and Humidity Control
Certain industries, such as electronics manufacturing and biopharmaceuticals, require precise control over temperature and humidity levels. In such cases, airflow control is vital for:
Uniform Distribution: Even distribution of conditioned air helps maintain consistent temperature and humidity throughout the cleanroom.
Preventing Condensation: Proper airflow prevents moisture buildup, which can lead to condensation and potential contamination in sensitive processes.
Comfort and Safety: Adequate ventilation and temperature control ensure that personnel can work comfortably for extended periods without compromising product quality or safety.
2.3.4 Energy Efficiency
Efficient airflow control not only enhances contamination control but also contributes to energy savings. Softwall cleanrooms are equipped with energy-efficient HVAC systems that:
Optimize Airflow: Advanced control systems adjust airflow rates based on real-time conditions, reducing energy consumption during periods of lower demand.
Minimize Air Change Rates: By strategically controlling airflow patterns and pressure differentials, cleanrooms can achieve the required cleanliness levels with fewer air changes, resulting in energy savings.
Section 3: Design Considerations for Effective Airflow Control
3.1 Planning and Layout
The design and layout of a softwall cleanroom play a pivotal role in achieving effective airflow control. Considerations include:
Workflow: Understanding the workflow within the cleanroom helps determine the placement of equipment, personnel, and critical processes, influencing airflow patterns.
Zoning: Dividing the cleanroom into different zones with varying cleanliness requirements allows for tailored airflow control strategies.
Entry and Exit Points: Properly designed gowning and degowning areas minimize the risk of contamination from personnel entering or exiting the cleanroom.
3.2 Airflow Patterns
The choice of airflow pattern depends on the specific requirements of the cleanroom:
Laminar Flow: Ideal for applications requiring high cleanliness levels, laminar flow directs air in a unidirectional, parallel manner. This reduces the risk of particle entrainment.
Turbulent Flow: Turbulent airflow is suitable for less stringent applications where rapid air mixing helps maintain uniform conditions.
Combination Flow: Some cleanrooms use a combination of laminar and turbulent flow to balance cleanliness and energy efficiency.
3.3 Filtration and Ventilation Systems
HEPA Filters: The selection and maintenance of HEPA filters are critical. Regular testing and replacement ensure that the filters function at peak efficiency.
Adjustable Dampers: Adjustable dampers enable fine-tuning of airflow rates in different zones, optimizing contamination control.
3.4 Monitoring and Control Systems
Modern softwall cleanrooms are equipped with advanced monitoring and control systems that offer real-time data on environmental parameters. These systems can automatically adjust ventilation, filtration, and temperature to maintain optimal conditions.
3.5 Personnel Training
Effective contamination control also relies on personnel following proper procedures for gowning, movement, and conduct within the cleanroom. Training programs are essential to ensure that employees understand and adhere to these protocols.
Section 4: Compliance and Validation
4.1 Regulatory Compliance
Industries that rely on softwall cleanrooms, such as pharmaceuticals and biotechnology, must adhere to strict regulatory standards. Regulatory bodies like the FDA and ISO have specific requirements for cleanroom design, operation, and monitoring. Compliance is essential to ensure product quality and safety.
4.2 Validation and Testing
Regular validation and testing of cleanroom performance are essential to confirm that contamination control measures are effective. This includes particle counting, air velocity measurements, and pressure differential testing. Validation ensures that the cleanroom consistently meets the required cleanliness standards.
Section 5: Conclusion
Airflow control in Softwall cleanrooms is a multifaceted and critical aspect of contamination control. By understanding the principles, components, and design considerations involved, industries can create environments that maintain the highest levels of cleanliness and safety. Whether it’s particle, microbial, or environmental contamination control, effective airflow management is the key to success in Softwall cleanroom operations.
Cleatech LLC, a leading provider of cleanroom equipment and solutions, offers a wide range of products designed to enhance contamination control in Softwall cleanrooms. From HEPA filtration systems to custom cleanroom enclosures, Cleatech is committed to helping industries maintain the highest standards of cleanliness and compliance.
In conclusion, airflow control in softwall cleanrooms is not just a technical requirement but a critical element in safeguarding product integrity, worker safety, and regulatory compliance. The meticulous design, implementation, and maintenance of airflow control systems are investments that pay dividends in terms of quality assurance and customer trust, making them an indispensable aspect of modern industrial processes.